Tour button
IAAPA Ride Safety Reports
Insights that empower safe adventures—IAAPA is the premiere source of global attractions research.
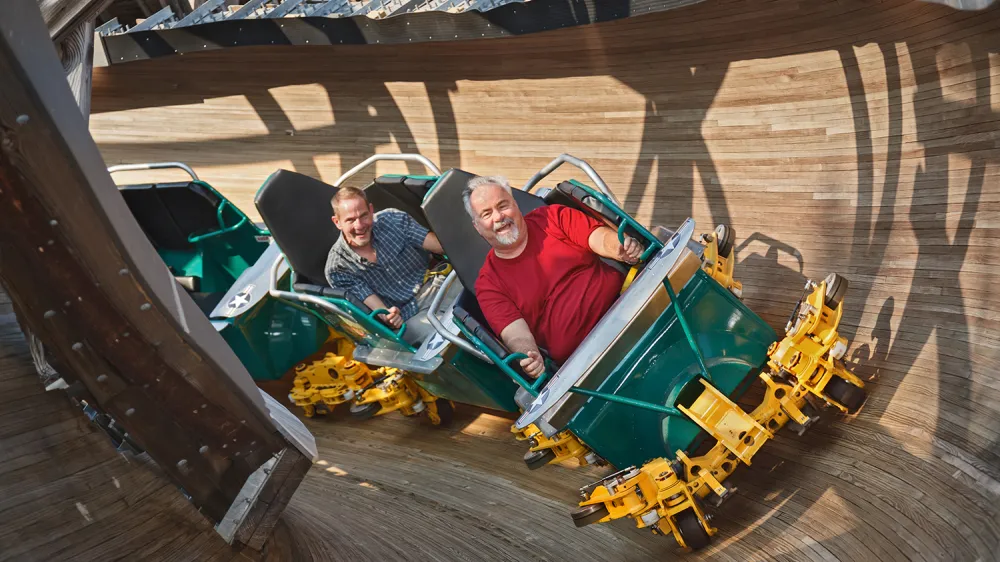
Mission Vision
Safety is a top priority
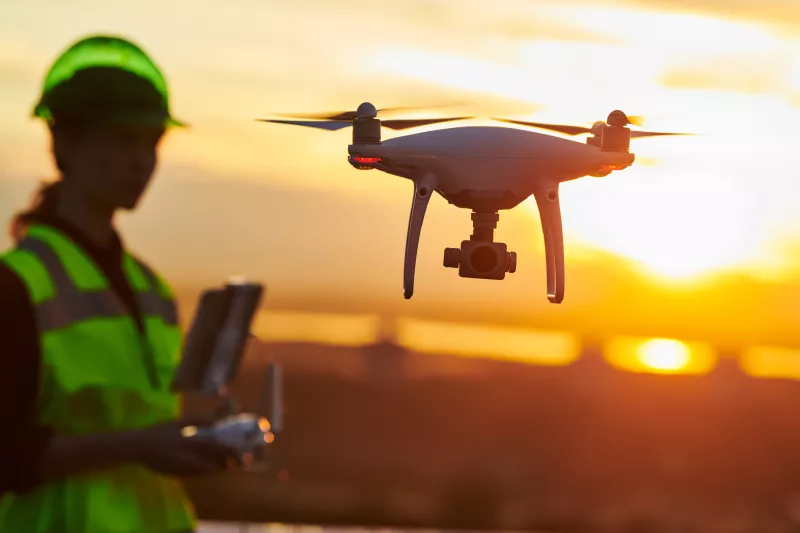
Safety is a key part of the industry’s priorities and amusement rides in the U.S. are extremely safe.
- In a typical year, more than 385 million guests safely enjoyed in excess of 1.7 billion rides at approximately 400 North American fixed-site facilities.
- The chance of being seriously injured on a fixed-site ride at a U.S. amusement park is 1 in 15.5 million rides taken.
- One injury is one too many and the industry is continuously working to enhance all aspects of safety.
Safety Fact Sheets
Expand allSafety is the Amusement Park Industry's No. 1 Priority
Safety is a partnership between an amusement park and its patrons. Unfortunately, a majority of the injuries occur because the guest didn't follow posted ride safety guidelines or rode with a pre-existing medical condition.
IAAPA created a list of amusement ride safety tips for guest use:
- Obey listed age, height, weight, and health restrictions.
- Observe all posted ride safety rules, and follow all verbal instructions given by ride operators or provided by recorded announcements.
- Keep hands, arms, legs and feet inside the ride at all times.
- Secure all loose articles, including wallets, change, sunglasses, cell phones, and hats.
- Do not board a ride impaired.
- Remain seated in the ride until it comes to a complete stop and you are instructed to exit.
- Always use safety equipment provided and never attempt to wriggle free of or loosen restraints or other safety devices.
- Parents should make sure their children can understand and follow safe and appropriate ride behavior.
- Never force anyone, especially children, to ride attractions they don’t want to ride.
- If you see any unsafe behavior or condition on a ride, report it to a supervisor or manager immediately.
- One G is equal to the normal pull of earth’s gravity on the body.
- Modern-day ride designers employ a steady stream of advances to create new, unique, and safe amusement rides and attractions.
- Amusement ride manufacturers applied the industry's biodynamic knowledge (collected over years) as it relates to g-forces to the design and construction of rides to ensure a safe experience.
- While technological gains have led to the development of bigger and faster rides, overall g-force levels have generally remained the same because riders’ tolerance levels have not changed.
When discussing the effects of g-forces on a person who is on a ride, the duration of the g-force and a multitude of other variables must be considered. When it comes to the higher–g sections of amusement rides, exposure often lasts fractions of a second. Therefore, the rider does not experience any adverse effects. Blackouts and other health issues associated with Gs require exposure to g-forces which are either greater in magnitude or of much longer duration than those achieved by today’s amusement rides.
- A study by Murray Allen, MD, Ian Weir-Jones, P. Eng, PhD, and several other doctors and engineers was published in the November 1994 edition of Spine.
- The study “found that in one event of daily activity, the vector acceleration of 10.4 g was experienced uneventfully.”
- Our bodies are exposed to greater gravitational pull during our everyday lives than that of an amusement park ride.
Examples of everyday gravitational forces:
Everyday Action/Gravitational Forces
- Sneeze: 2.9
- Cough: 3.5
- Crowd Jostle: 3.6
- Slap on the Back: 4.1
- Hop off a Step: 8.1
- Plop Down in a Chair: 10.1
- At least five independent scientific reviews have analyzed the issue of amusement ride g-forces, and all five have concluded: The rotational accelerations experienced by the head during rides pose no risk of brain injury to the general populace.
- A focus simply and strictly on the matter of g-forces or height or speed is wholly inadequate when discussing the physical experience of riding a roller coaster or any other amusement ride.
- These reviews demonstrate that the dynamic characteristics of the interaction between ride and rider is far below even the minimum levels associated with brain injury.
- ASTM International has incorporated g-force limits into its ride safety standards that guide the amusement industry.
Technological Advancements Result in Safer Experiences:
- The design and development of amusement rides requires a mastery of physics, engineering, and mathematics.
- As technology has improved to include computers, advanced materials, and certain design innovations, the result has been an increasingly rigorous, complex, and precise creative process.
- This process has contributed to an extraordinary safety record proving amusement rides are one of the safest forms of recreation available to the public.
- The amusement park industry's tradition of continual improvement greatly enhances ride safety. For example, the introduction of force reactive supports, headrests, comfort padding, seat dividers, ratcheted restraints, computer controls, and magnetic braking systems.
- Modern-day ride designers employ a steady stream of advances to create new, unique, and safe amusement rides and attractions.
- Amusement ride manufacturers applied the industry's biodynamic knowledge as it relates to G-forces to the design and construction of rides to ensure a safe experience.
- While technological gains have led to the development of bigger and faster rides, overall G-force levels have generally remained the same because riders’ tolerance levels have not changed.
Time-Tested Technological Principles and breakthroughs:
- Fail-safe defaults ensure in the case of a power outage or other external event, vehicles come to rest in a safe position and remain there until passengers are evacuated according to a pre-arranged plan or the ride is re-started
- Redundant safety mechanisms in critical areas provide backup in case the primary system malfunctions.
Impact of the computer:
- Perhaps the most crucial advancement is the computer and its far-reaching impact on ride design, manufacture, and operation.
- Designers employ modeling software to manipulate a large number of elements quickly and easily, optimizing a ride’s final layout, and providing a complete analysis of its performance, structural integrity, and g-force parameters.
- The fabrication of various ride and attraction components are now even more technically precise.
- Park personnel use central control units and numerous high-tech sensors to constantly monitor all aspects of a ride. Mid-ride adjustments, activation of themed elements, and automatic system shutdowns occur faster and more accurately.
Amusement Ride Enhancements:
- Roller coaster manufacturers are still exploring the possibilities that opened to them with the advent of tubular steel tracks and polyurethane wheels.
- Lightweight fiberglass and plastics has contributed to the improvement of various rides and attractions, including carousels, animatronics, and bumper cars.
- Several types of amusement rides, especially roller coasters, employ vibration-dampening material to provide structural enhancement.
- “Locking” roller coasters on the track via a three-wheeled device (top, side, and bottom) produces a whole new world of twists, turns, and inversions.
- Modern catapult-type launch systems powered by pneumatics and linear electric motors have expanded the creative options available to ride manufacturers.
- The integration of special effects, motion simulation, and/or theming within ride environments has resulted in a wider array of guest experiences.
- Amusement park standards are set by the ASTM International, F24 Committee on Amusement Rides and Devices
- ASTM F24 is comprised of consumer advocates, government officials, amusement park operators, ride manufacturers, and industry suppliers.
- The committee establishes standards on design and manufacture, testing, operation, maintenance, inspection, quality assurance, and more.
- These standards undergo frequent review and revision to keep up with new technologies, and have been adopted by many governmental jurisdictions.
- Amusement parks are subject to state and local governmental codes, requirements, and safety inspections, and must pass rigorous inspections by insurance companies.
- If regulations in specific states need to be augmented, IAAPA encourages such action and recommend using the detailed ASTM International ride safety standards as the basis of any regulations.
- Amusement park staff follow detailed manufacturer guidelines for inspection and safety, and many parks use outside specialty companies to periodically re-inspect rides. These inspections take place on a daily, weekly, monthly, and yearly basis.
- ASTM International standards require fixed-site amusement industry operators and manufacturers report both incidents and ride-related defects, including notification of facilities when a ride develops a manufacturer-related safety issue.
North America Ride Safety Information:
- Currently 44 of 50 states regulate amusement parks. The six without state oversight are Alabama, Mississippi, Montana, Nevada, Wyoming, and Utah. These states contain few, if any amusement parks.
- Then-Congressman Ed Markey convened a panel of leading doctors, biodynamic consultants, medical experts, and ride safety specialists to study the amusement park industry's safety record. The panel concluded it is unlikely that a federal agency could match the effectiveness of the current system.
- Relevant data consistently shows only a small percentage of incidents that do occur are caused by factors subject to governmental ride operations oversight, namely either staff or mechanical error.
1981 CPSC's authority examined:
- Like several court cases prior to that time, Congress determined that fixed-site amusement rides could not be considered household products, are not within the consumer’s control, and are constantly maintained by a team of experts.
- Congress concluded that the facility buys the product and the consumer buys the associated experience.
- The CPSC acknowledged any effort to expand the agency’s jurisdiction to include fixed-site amusement rides requires increasing the agency's staff and budget.
- Amusement parks continue to report incidents to state and local governments and partner with government officials and inspectors to ensure the safety of their guests.
Fundamental safety measures have been in place for decades:
- In addition to a thorough set of internal mechanical, electrical, design, and operational safety checks and standards, fixed-site amusement rides are subject to one or more layers of independent examination: state and local government, insurance companies, and private safety firms.
EU Standards:
After several years of work and industry collaboration, experts organized in the technical committee CEN/TC152 have agreed on an update to the European Standard EN 13814. This change came into effect on June 1st, 2019. The standard is split up in 3 parts:
- EN 13814-1:2019 Safety of amusement rides and amusement devices - Part 1: Design and manufacture
- EN 13814-2:2019 Safety of amusement rides and amusement devices - Part 2: Operation, maintenance and use
- EN 13814-3:2019 Safety of amusement rides and amusement devices – Part 3: Requirements for inspection during design, manufacture, operation and use
It represents the “state of the art” on amusement ride safety in Europe and continues its predecessor’s (EN 13814:2004) role as one of the key global standards for ensuring amusement ride safety. The new standard also marks a step forward in the harmonization efforts with ASTM, thanks to the collaboration between CEN and ASTM experts.
EN 13814:2019 has currently been adopted by more than 40 Countries across the world, either as a whole or as a partial reference.
- Restraints vary according to both their design and ride type, thus allowing a significant level of specialization, including the widespread use of individually-adjustable restraints.
- Restraint design is typically based upon a 95th percentile physical profile to comfortably accommodate the vast majority of a ride’s population segment.
- Manufacturer guidelines help parks address guests whose physical attributes are outside the design parameter due to size, disability, or other factors. Such actions can include adjusting the seating location of certain patrons.
- Many parks provide information regarding the issues of size and disability through signage, printed or web materials, and “test yourself” seats, as a courtesy, at the start of queue lines.
- Restraints undergo rigorous testing in the design phase, and industry guidelines are continuously reviewed through the ASTM process.
- Restraints are tailored to handle the intended forces of a ride and the reasonably foreseeable actions of its riders.
- There are often at least two restraint devices on a ride, and any restraint is just one part of a ride’s overall safety measures.
- Information on restraint changes or updates is shared through the ASTM International standards development process, industry forums (education seminars, etc.), and ASTM protocols for manufacturers to inform parks of ride-related safety changes and via state/local agencies data exchanges.
Ride Operator Training
- Amusement parks provide one of the safest recreational activities for the public. Properly trained ride personnel are an important part of providing guests with a fun and safe visit.
- The amusement park industry uses formalized policies, procedures, and programs for operations, including in the area of training park personnel.
- Employees are trained using procedures established by the facility working together with manufacturers and insurers, and in accordance with relevant public laws.
- IAAPA provides training products, including education sessions, webinars, manual, videos, and safety seminars and workshops where the latest standards and techniques are shared and discussed.
- Information from other industry groups and advisory bodies like ASTM International are used. These processes are constantly documented, standardized, practiced, and upgraded.
- Front-line personnel are screened for important characteristics; such as the polite but firm assertiveness needed to ensure that ride rules are followed. This deliberate and sequential manner extends to staff development. Staff instruction begins before training to be operators as admission or loading attendants and continues to operators of simple rides who are brought along step-by-step before graduating to more complex rides.
- Training is on a continual basis and includes: operations, admissions, ride systems, accessibility for guests with disabilities, maintenance, and emergency procedures.
- Amusement ride operators receive training through “hands-on” instruction with more experienced staff, case studies, structured drills, group discussions, and/or seminar presentations.
- Facilities document and validate the training.
- Parks and attractions work with manufacturers and others to develop a range of manuals, checklists, and logbooks in establishing an operational program for each amusement ride. Only after employees earn the required authorization through this training process are they then permitted to staff an amusement ride.
- Trained and qualified ride operators and attendants are only one element in a facility’s total safety program. Together with a ride’s redundant safety and operational mechanisms that reduce the likelihood of staff error, various daily internal checks, and one or more outside inspections, front-line personnel help make amusement rides one of the safest forms of recreation available to the public.
- Through “Guest Relations” offices, signage, and verbal directions, parks work to enlist their visitors as partners in enjoying rides safely and correctly.
Age of Amusement Ride Operators
- IAAPA is aware of no data linking younger amusement ride personnel to a higher rate of amusement ride incidents for either guests or staff.
- Amusement ride operator training and experience is key – not age or other arbitrary criteria.
- 29 states have a law to set a minimum age for amusement ride personnel, and three more have established other employee requirements for these staff.
- Amusement parks and attractions have formalized and validated training procedures, and only after employees earn the required authorization through this training process are they permitted to staff an amusement ride.
- Amusement ride staff are complemented by numerous other safety practices, and a small percentage of incident are caused by either staff or mechanical error.
- In most states at 16, young adults are eligible to drive, lifeguard, and hunt – compelling evidence that 16 is an equally appropriate age to work as amusement ride staff.
- By federally limiting amusement ride personnel to 18 and older, this equates such work with manufacturing explosives, coal mining, sawmilling, handling radioactive substances, and demolition operations. There is a big difference between staffing an amusement ride and those activities.
With the proliferation of personal devices including cell phones, cameras, and “selfie sticks” the long-standing industry policies restricting loose articles from rides and attractions should be reviewed. “Selfie sticks” have proliferated as a natural outcome of ballooning global engagement in social networking using still and video imagery. A “selfie stick” is an expandable stick which a person attaches to a mobile phone or camera to help take a selfie (a photo of oneself and possibly others). It can be collapsed into its handle, becoming small and portable.
Almost all rides and attractions advise guests to “hold on” and provide specific bars or other implements, which guests should grasp as needed. Distraction from this should be avoided as much as possible which any loose articles including the personal devices mentioned above may create, in addition to being potentially dangerous to other patrons if they are not secured or fall from a patron’s grasp.
Most rides are designed with specific ASTM, EN, or other ‘standard-defined’ reach envelopes in mind. These reach envelopes assume large, adult humans are trying to reach outside the ride vehicle, and the standards ask the designers to consider and mitigate this possible hazard. None of these standards assume that riders will be carrying “reach extenders” on board with them. Canes, crutches, umbrellas, and the like have long been prohibited on most rides because of reach envelope hazards, and/or hazards that arise if such objects become loose in the ride vehicle or device during more dynamic motion.
We remind ride owner/operators that they should enforce the safety criteria cited by the rides' designer/engineers, including the management of reach envelope from the ride vehicle or device and from nearby its perimeter. The IAAPA Safety Committee strongly suggests that selfie sticks should be held to the same prohibition criteria as (e.g.) umbrellas for any hazardous scenarios on or near rides.
Also we recommend consideration of other safety situations potentially changed by the introduction of selfie sticks in non-ride environments. Proximity to performers, animal compounds, dense crowd situations, where safety may be affected by the presence of these devices and risks posed to persons and property including valuable museum or other historic objects.